By: Ben Boslaugh—Missouri State University
There are likely several hundred or more on your campus, but are they properly sized? Pressure gauges typically have the specified isolation valve (or trumpet valve), snubber, or pig tail. Proper sizing can present serious issues when miscalculated. The accuracy of the gauge is not always what is shown on the gauge face. Most bourdon tube mechanical pressure gauges are accurate between 1/4 and 7/8 of the gauge range. It is not a linear relationship. For example, the gauge shown to the right would be most accurate between 15 psi and 52.5 psi.
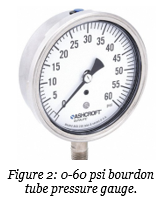
One may wonder why this is important. Below is a photo of a failed hydrostatic test on a section of 12” C-900 chilled water piping. There were several contributing factors to the catastrophic failure of the pipe. However, the most significant was the selection of the pressure gauge. The test was to 160 psi. The gauge selected was a 0-160 psi pressure gauge. The effective gauge range of the 0-160 psi gauge was 40-140 psi. The pressure applied to the piping was much higher than the specified 160 psi due to the pressure gauge being “topped out”. No one was injured and repairs were quickly facilitated.
A 0-200 psi gauge would have been the minimum acceptable gauge for the test.
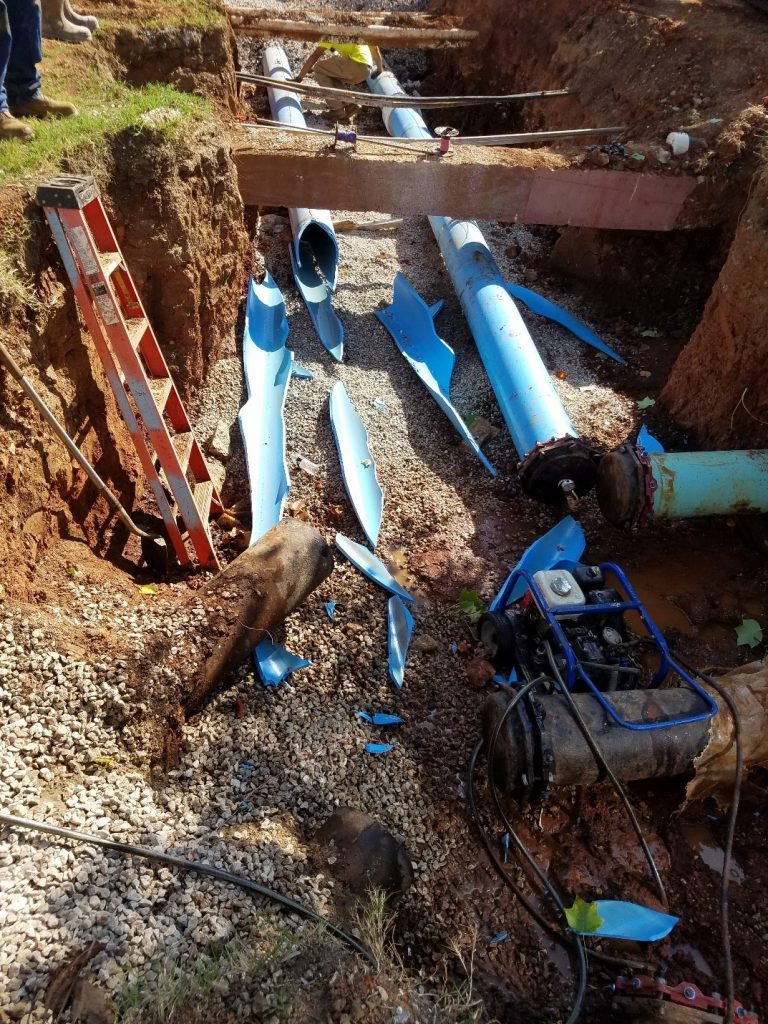
Figure 2: Failed section of 12" C-900 Chilled Water Piping.